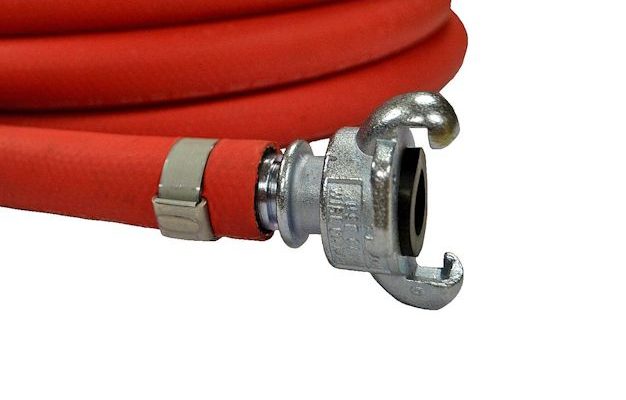
A word (or a few) on working pressure ratings:
Rubber industrial hose is typically marked by the manufacturer with the working pressure rating directly on the hose. This is calculated based on a burst test at the factory, without taking into account what couplings will be installed, how they will be installed, and how the hose will be used. Because of these factors, the actual assembly rating may be much different than what is stated. For example, air hose is typically rated at 200 or 300 PSI and therefore will state this along the hose layline, but the hose assembly pressure is often much lower…
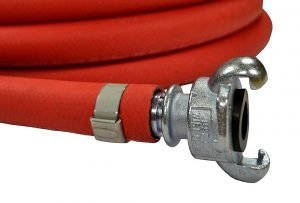
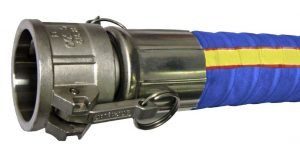
Additional factors can decrease working pressure rating including temperature (inside the hose and out) and stresses such as end pull or pulsation. A hose hung from its coupling without any bracing or support and under pressure can cause a failure even when operating within the hose assembly’s capable pressure range. Elevated temperature can reduce an industrial hose working pressure by more than half. Refer to the chart and additional info here.
All of these factors can reduce the rating marked on the hose significantly. Determine your safe operating pressure limit, inform all potential users of the hose assembly, and tag the assembly with its proper rating. Also keep in mind that a used hose may not perform as well as a new hose, even if it appears to be in serviceable condition. If an application will be near the peak of an assembly working pressure, consider installing a new hose for best performance.
Install hose safety cables or whip checks to reduce the risk of injury if an accident were to occur. Inspect hoses regularly as well, and remove them from service BEFORE they fail.